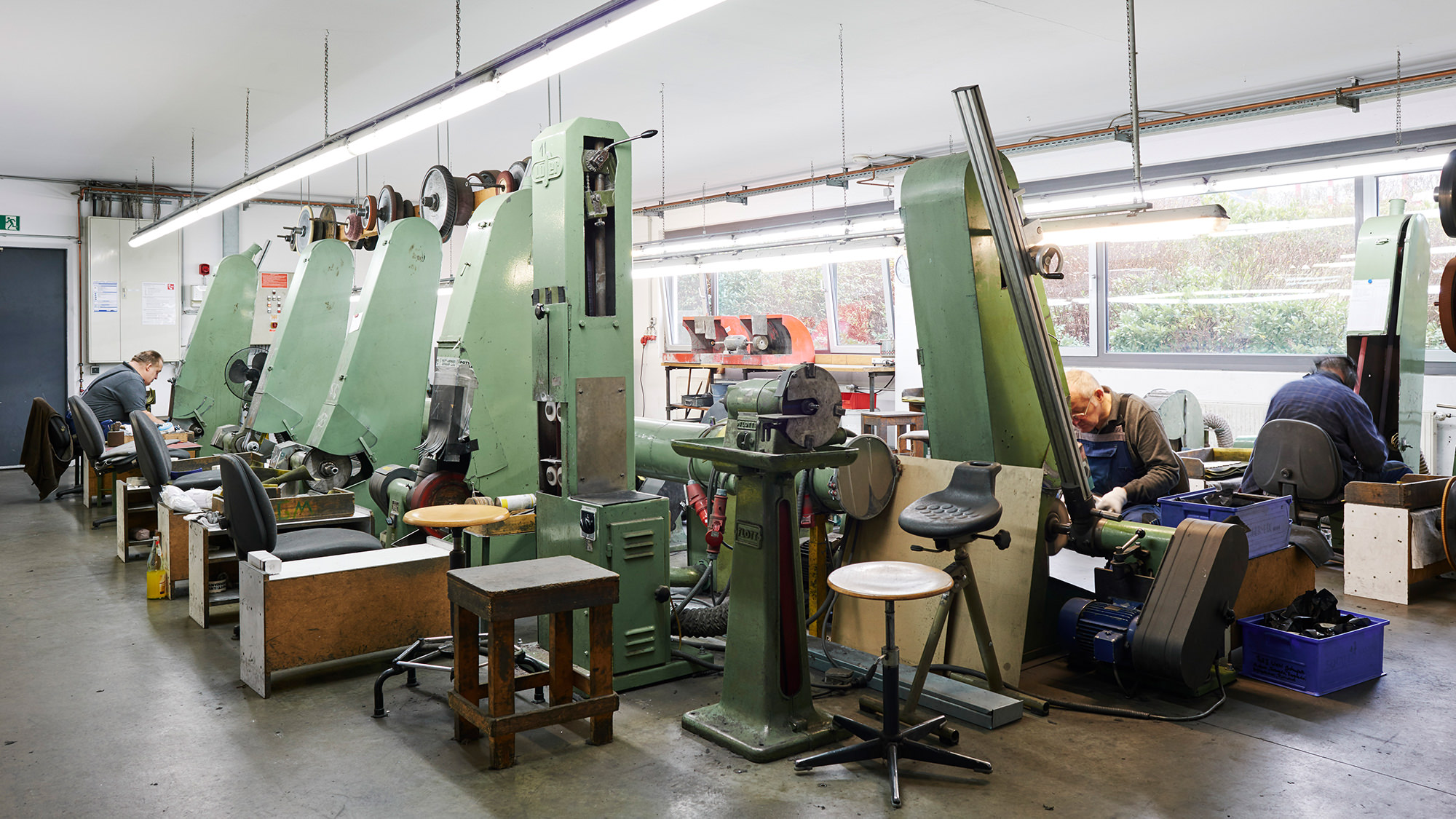
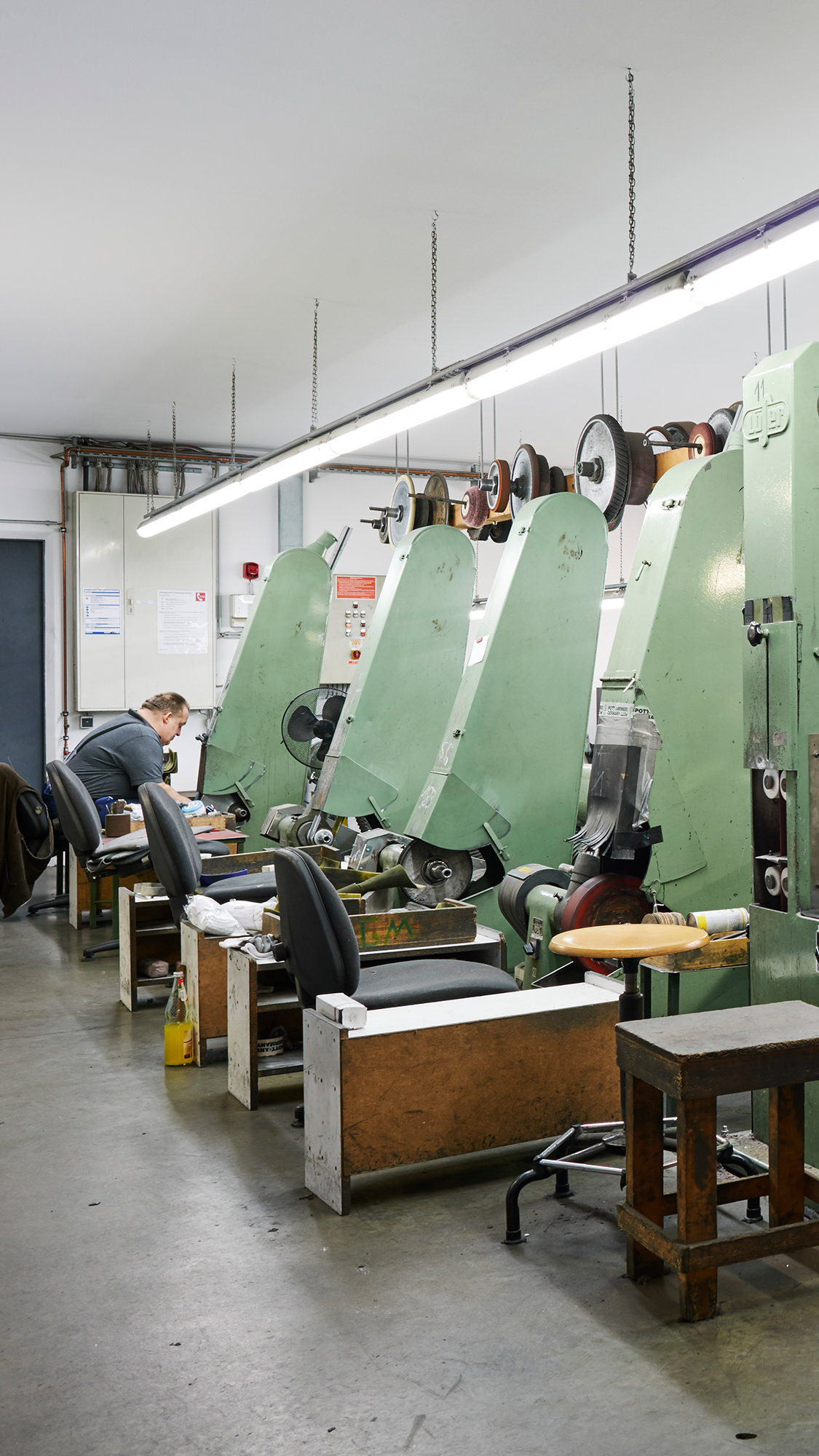
Only when perfection has been achieved through the final touch does a Pott flatware leave the manufactory.
All Pott and Mono flatware is manufactured in the Mono manufactory in Mettmann. Before you hold one of them in your hands, it has passed through the experienced hands of our master craftsmen, who with infinite patience and care work each piece until it meets the highest quality standards. The traditional craftsmanship techniques have been refined over the decades. Deburring, smoothing, sharpening, sanding, polishing, brushing, grinding, and in between, pausing and checking again and again. A spoon and fork each require more than 30, a knife requires more than 90 work steps. The result of this immense effort is the quality and durability of each Pott and Mono flatware. On this page we would like to explain the complex process of flatware production step by step.
Material
For the production of Pott flatware, stainless steel sheets in thicknesses from 0.8mm to 4mm are used. We use cold rolled, brushed or shiny material, depending on the intended use. With the exception of the knife blades, we manufacture all stainless steel flatware from 18/10 stainless chrome-nickel steel. The knife blades are made of other hardened blade special steels. The stainless steel plate is delivered as a plate with a size of 100 x 200cm. From one tablet about 400 forks or 800 coffee spoons can be made. For sterling silver flatware, we use 100 x 50cm bars. These plates are not in stock, but are ordered and processed according to the order. Silver is about 30% heavier than stainless steel.
Guillotine shear
When cutting the stainless steel sheets with the guillotine shears, the sheet is cut straight between a fixed and a movable knife in one operation. The maximum cutting length is two meters. The maximum material thickness is 5mm. Each piece of flatware has a pre-defined strip width to ensure optimum use of the material. Cutting with the guillotine shears requires two employees to ensure that the cut stainless steel strips do not scratch when they fall out.
Brandel cut
At the eccentric press, the "Brandeln" (flatware blanks) are punched from the stainless steel strips at a pressure of 65 tons per square centimeter. The shape of the Brandel does not usually indicate whether it is a table spoon or fork blank, for example, since the cut is often the same. The "setup time" of the press is about 20 minutes for each piece of flatware, since it has to be adjusted very precisely.
Pre-grinding
Since each cutting operation causes a burr on the brandel, each brandel must be pre-ground by hand after cutting. This operation can be repeated up to three times during production. If pre-grinding were to be omitted, this would result in damage to tools or inaccuracies in the individual flatware pieces. Since the pre-grinding of the brandeln produces fine grinding dust that sticks to the surface, the brandeln are cleaned again afterwards.
Stamping
At the stamping machine, an eccentric press with a pressure of 8t/cm2, the Pott logo, material information and if necessary the designer is stamped into the back of the brandel.
Rolling
At the roller, the upper parts of the spoon and fork are rolled thinly to the desired dimensions. Per brandel 16 - 30 rolling passes are necessary to obtain the desired material thickness. Forks are rolled to a thickness of 1.8 - 2.0 mm, the spoon to a thickness of 1.2 - 1.5 mm. This gives the flatware a good balance and the tops lie comfortably in the mouth.
Cutting
With a pressure of 55t/cm2, this eccentric press cuts the rolled top part of fork and spoon to obtain the final contour. After this operation, the workpiece is ground and cleaned again.
Tines cutting
The tines are punched out of the fork blank in two operations at a pressure of 25 - 30t/cm2. In the case of a 4-tine fork, the middle tine is punched first and then the two outer tines. In the case of a 5-tine fork, two tines are punched at a time. If one were to attempt to punch out all the tines at once in a single work step, the material would twist.
Embossing
With a pressure of 600 - 800t per cm2, this machine presses the brandel into its final three-dimensional shape. During this operation it is essential that the brandel is one hundred percent clean. Before pressing, each individual part is cleaned by hand. A single grain of dust or a hair on the stainless steel surface would have fatal consequences when pressing at this high pressure and leave deep marks that cannot be removed.
Edge sanding
Edge grinding starts with the flatware tops. The fork with its tine gaps is particularly complex. First a rough 120 grit is used, in the second course a fine 320 grit and sanding paste. When sanding the edge of the flatware handles, the grinder usually has the possibility to process several pieces at the same time. This technique is called "package sanding".
Sisal disc
When grinding the top and bottom surfaces of the flatware pieces on the sisal disc, white grinding paste is used, which the grinder repeatedly applies. As a result, some material is ground from the flatware part, which removes irregularities and leaves a slight shine.
Matting
To finish a matte flatware item, the surface is treated with a fibre brush and brown grinding paste. This special matting brush is made of fibers that are made from leaves of the Algarve plant. The brown grinding paste with its soft, greasy consistency ensures that a slightly silky shine is created in the matting.
Polishing
When finishing a polished flatware item, the grinder uses brushes made of soft cotton cloth and a fine pink grinding paste. The flatware is polished until a high gloss is achieved. During the polishing process, the grinder wears cloth gloves so that the flatware is not scratched again.
Insertion
The Pott knife blades are forged by hand in a manufactory in Solingen using traditional manufacturing methods. Back at the manufactory in Mettmann, the blades are inserted into the handle, this work step is called "Reiden". During this process, the hollow handle is filled with quartz sand, which allows for a particularly balanced weight of each knife.
Knife grinding
In the grinding shop, the transition between the handle and the blade is worked on. The handle is then given its final finish. In the "scotching" process, the blade surface is freed from scratches and grooves without removing material, which increases the cutting quality. The Pott-specific micro-serration, a saw grind that is barely visible to the naked eye, guarantees high, long-lasting sharpness.
Ultrasonic cleaning
The finished matted or polished flatware pieces are carefully placed in wooden boxes and then go to the washing line for ultrasonic cleaning. There, the greasy residues of the grinding pastes are washed off.
Confection
Every piece of flatware is cleaned by hand and checked for its perfect appearance before it is packed and stored.
Learn more about...